Design
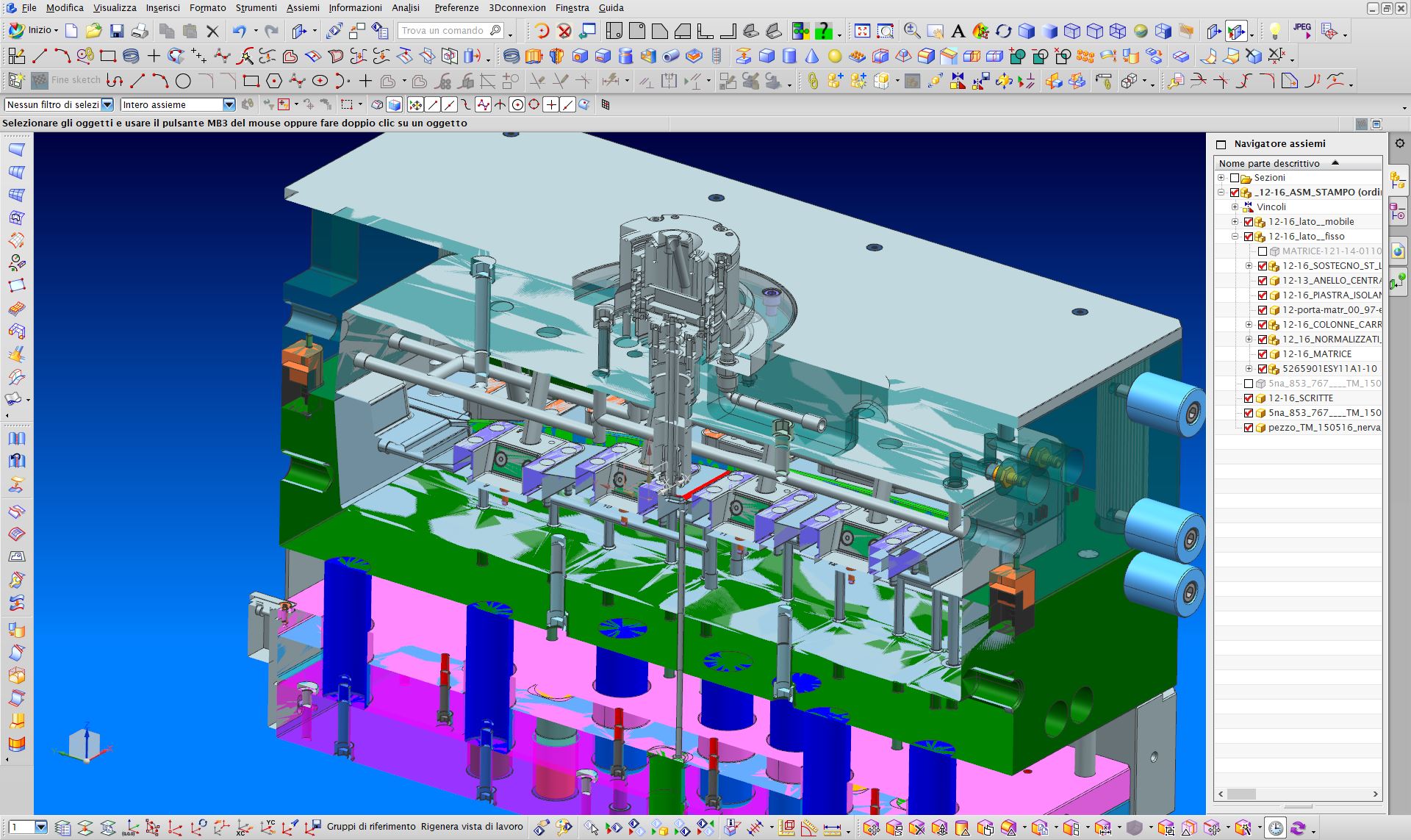
In the design office, ideas take shape: the design of the part, in collaboration with the customer, and the mould, are carried out internally by a team with many years of experience, and through 3D-CAD systems always updated to the latest version available.
The activity begins with the preliminary ‘Project brief’ where the annual volumes to be produced are defined, the material is chosen together with the technical and aesthetic specification of the component, the target cost, the planning and timing of the sampling are set.
After the definition of parts details, it is possible to produce samples obtained with rapid prototyping techniques, which allow to “touch” the component already in a preliminary phase and thus prevent mistakes in the concept of the piece, and eliminate the risk of increased costs for the moulds to be constructed.
The activity then focuses on the design of the mould, which begins with the determination of the number of cavities and follows with the choice of the injection system and the definition of the position and number of injection points, to then continue with the study of the cooling system and the ejection system.
The technical choices are always shared and available for the customer. If a maquette is already available, TecnoMas is able to obtain the mathematics of the piece through reverse engineering studies.
Before starting the production of the mould, where necessary, the structural analysis and mould flow are carried out.
At the end of the construction of the mould follows the sampling activity: the PPAP approval process (Production Part Approval Process) is supported by metrological reports according to the needs and requests of the customer, till the approval of the component and equipment.
The complete management of each project is leaded by a project leader, as single technical point of contact for the whole duration, up to the sampling and approval phase, thus guarantees optimal planning control, reduction of time, flexibility and maximum reactivity, to all advantage of the timing and costs of the project.
3D drawings and 2D views are available for the customer and allow, even years later, to be able to operate on the mould, for modification or maintenance activities, having the mould structure very clear.
Where post-moulding activities are foreseen, such as assembly and gluing, the TecnoMas Design office is able to provide support for the production of gluing mask and other ancillary equipment.